දියමන්ති කියත් තලය, පාලම් ඇලුමිනියම්, ඇක්රිලික් සහ ගල් කැපීම සඳහා බහුලව භාවිතා වන බහු තල මෙවලමකි.ලෝහ කැපීම සමස්ත ඉතිහාසය තුළ, දියමන්ති කියත් තල මතුවීම දෘඪ මිශ්ර ලෝහ කියත් තල සහ කාබන් වානේ කියත් තල බොහෝ අඩුපාඩු සඳහා ඵලදායී ලෙස වන්දි ලබා දී ඇත.
විශිෂ්ට කැපුම් කාර්ය සාධනය දියමන්ති කියත් තලවල ආවේණික වාසියක් වන අතර, දැඩි හා වඩා තාප ප්රතිරෝධී දියමන්ති කියත් දත් භාවිතය හේතුවෙන් දියමන්ති කියත් තලවල ආයු කාලය ද ඉතා දිගු වේ.
සාමාන්ය දෘඩ මිශ්ර ලෝහ කියත් තල හා සසඳන විට දියමන්ති කියත් තලවල ආයු කාලය බොහෝ විට මාස කිහිපයක් වැඩි වේ.ඇත්ත වශයෙන්ම, දියමන්ති කියත් බ්ලේඩ් වල ආයු කාලය කෙරෙහි බලපාන බොහෝ සාධක තිබේ.
කියත් තලයේ ගුණාත්මක භාවයට අමතරව, සැබෑ නිෂ්පාදන ක්රියාවලියේදී, දියමන්ති කියත් තල භාවිතය සහ ක්රියාකරුගේ ක්රියාකාරිත්වය ප්රමිතිගත කර තිබේද යන්න මෙන්ම පෝෂණයේ ගැඹුර සහ රේඛීය වේගය ද සේවා ජීවිතයට බලපානු ඇත. දියමන්ති කියත් තලය.
වර්තමානයේ, නිෂ්පාදනය සඳහා බහුලව භාවිතා වන ක්රම හතරක් තිබේදියමන්ති කියත් තල, සීතල පීඩන සින්ටර් කිරීමේ ක්රමය, උණුසුම් පීඩන වෙල්ඩින් ක්රමය, රෝල් කිරීමේ ක්රමය සහ දත් කාවැද්දීමේ ක්රමය ඇතුළුව.
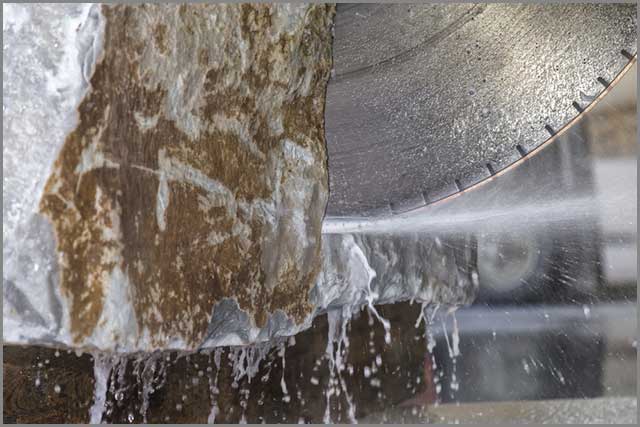
ක්රමය 1: සීතල පීඩන සින්ටර් කිරීමේ ක්රමය
සීමිත නිෂ්පාදන තාක්ෂණය හේතුවෙන් සීතල පීඩන සින්ටර් කිරීමේ ක්රමය මගින් නිපදවන දියමන්ති කියත් තලවල විෂ්කම්භය සාමාන්යයෙන් මිලිමීටර් 400 ට වඩා අඩුය.
මේ අතර, සීතල පීඩන සින්ටර් කිරීමේ ක්රමයට අඩු නිෂ්පාදන පිරිවැයේ වාසිය ඇත, විශේෂයෙන් සමහර තෙත් කියත් තල සඳහා.නිෂ්පාදන ක්රියාවලියේදී, සීතල පීඩන වෙල්ඩින් ක්රමය සාමාන්යයෙන් භාවිතා වේ.
එමදියමන්ති කියත් තලයමෙම නිෂ්පාදන ක්රියාවලිය භාවිතා කිරීම බොහෝ විට ග්රැනයිට්, මිශ්ර දෘඩ පස්, ඇස්ෆල්ට් වැනි දුෂ්කර පැතිකඩ කැපීමේදී ස්ථාවර ක්රියාකාරිත්වය සහතික කරයි.
ක්රමය 2: උණුසුම් මාධ්ය වෙල්ඩින් ක්රමය
දියමන්ති කියත් තල නිපදවන ව්යවසායන් සඳහා, ස්ථාවර නිෂ්පාදනයක් සහතික කිරීම සඳහා, ඔවුන් බොහෝ විට වර්තමානයේ උණුසුම් මුද්රණ වෙල්ඩින් ක්රමය තෝරා ගනී.
දියමන්ති කියත් තල නිෂ්පාදනය කිරීමේ මෙම ක්රමය දැනට වඩාත් ජනප්රිය ක්රමයයි.මේ අතර, සීතල පීඩන වෙල්ඩින් ක්රමයට සාපේක්ෂව, මෙම නිෂ්පාදන ක්රමය මඟින් විශාල විෂ්කම්භයක් සහිත දියමන්ති කියත් තල නිපදවිය හැකිය.
විෂ්කම්භය පරාසය සාමාන්යයෙන් මිලිමීටර් 350ත් 2200ත් අතර වන අතර ගල් කැපීමට භාවිතා කරන සමහර යෝධ දියමන්ති කියත් තල මෙම ක්රියාවලිය නිෂ්පාදන ක්රියාවලියේදී භාවිතා කරයි.මූලික නිෂ්පාදන ක්රියා පටිපාටිවලට මිශ්ර කිරීම, උණුසුම් පීඩන සින්ටර් කිරීම, චාප ඇඹරීම, වෙල්ඩින් සහ කැපීම ඇතුළත් වේ.
ක්රමය 3: රෝල් කිරීමේ ක්රමය
දියමන්ති කියත් තලරෝලිං ක්රමය මගින් නිෂ්පාදනය කරනු ලබන නිෂ්පාදන පිරිවැය සාපේක්ෂව අඩු වන අතර, මෙම නිෂ්පාදන ක්රියාවලිය මගින් නිපදවන දියමන්ති කියත් තල සාමාන්යයෙන් ඔරලෝසු, මැණික් ගල්, ෙබයාරිං වැනි කියත් ද්රව්ය සඳහා භාවිතා වේ.
මෙම ක්රමය භාවිතා කර නිෂ්පාදනය කරන ලද දියමන්ති කියත් තලය සාමාන්යයෙන් සෑදී ඇත්තේ ලෝහ තහඩු වලින් වන අතර විෂ්කම්භය මිලිමීටර් 80-120 අතර සහ ඝණකම මිලිමීටර් 0.2-0.4 අතර වේ.
ක්රමය 4: ගියර් ඇතුල් කිරීමේ ක්රමය
නමට අනුව, ඉන්ලේ ක්රමය වන්නේ කියත් තල උපස්ථරයේ දත් ආසනය මත දියමන්ති කියත් තැන්පත් කිරීමයි.මෙම නිෂ්පාදන ක්රියාවලියෙන් නිපදවන දියමන්ති කියත් තලය තුනී වන අතර, කියත් පිටත කවයේ අඛණ්ඩව දිස්වන අතර රෝද දාරයේ තදින් කාවැදී ඇත.කැපීම තියුණු වන අතර චිප්ස් ඉවත් කිරීමට පහසුය.
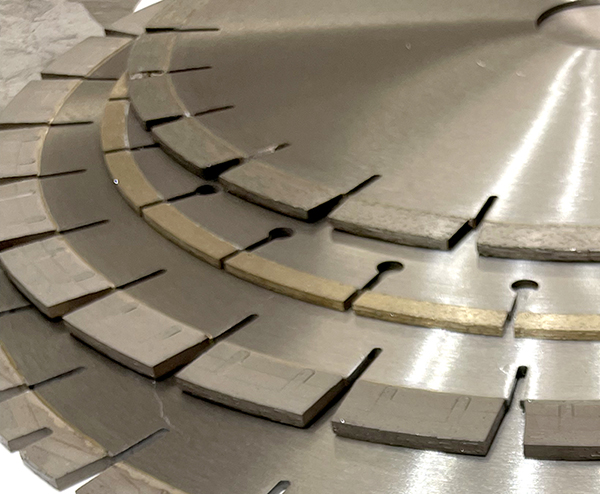
ඒ සමගම, කියත් බ්ලේඩ් සඳහා මෙම නිෂ්පාදන ක්රියාවලිය භාවිතා කිරීමේ වාසි වන්නේ ඉහළ කැපුම් කාර්යක්ෂමතාව, අඩු ද්රව්යමය පාඩුව සහ තුනී ද්රව්ය කැපීමේ හැකියාවයි.මක්නිසාද යත්, ගල් ක්ෂේත්රයට අමතරව, මෙම ක්රියාවලිය භාවිතයෙන් නිෂ්පාදනය කරන ලද කියත් තල ඇලුමිනියම් පැතිකඩ සැකසුම් ක්ෂේත්රයේ ද භාවිතා වේ.
වර්තමානයේ, භාවිතා කරන නිෂ්පාදන ක්රමය කුමක් වුවත්, දියමන්ති කියත් තලවල සහ කැපුම් පැතිකඩවල ගුණාත්මක භාවය ඵලදායී ලෙස සහතික කළ හැකිය.ඇලුමිනියම් පැතිකඩ සම්බන්ධයෙන් ගත් කල, උසස් නිෂ්පාදන ක්රියාවලිය හේතුවෙන්, කියත් තලයේ කැපුම් ක්රියාකාරිත්වය තරමක් විශිෂ්ටයි.
මීට අමතරව, විශිෂ්ට ලෝහ කැපුම් ලක්ෂණ නිසාදියමන්ති කියත් තල, ඔවුන් නැවත නැවතත් ගොඩක් බිම කළ හැක.
සාමාන්ය දෘඩ මිශ්ර ලෝහ කියත් තල හා සසඳන විට ජීවිත කාලය තුළ 1-2 වතාවක් පමණක් ඔප දැමිය හැකිය.දියමන්ති කියත් තලජීවිත කාලය තුළ 6-8 වතාවක් ඔප දැමිය හැකිය.ව්යවසායන් සඳහා, එයින් අදහස් වන්නේ ඇඹරුම් ක්රමයක් අනුගමනය කිරීමයි, එමඟින් විශාල පිරිවැයක් ඉතිරි කර ගත හැකිය.
පසු කාලය: දෙසැම්බර්-14-2023